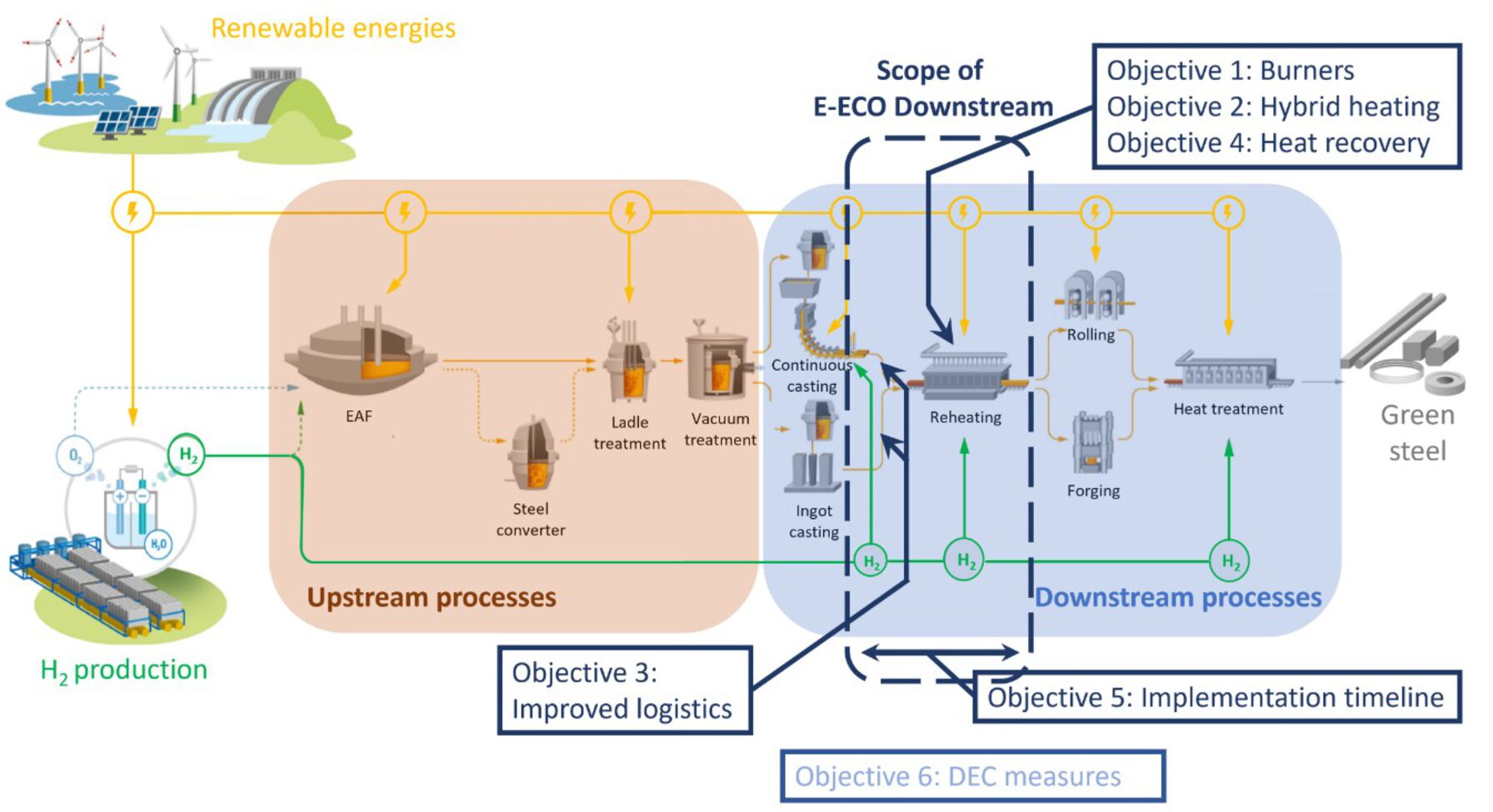
Objectives
The research work distinguishes four technical research topics:
-
- Fuel flexible burners for reheating surfaces,
- hybrid heating in reheating furnaces,
- improved logostic systems for increased efficiency and
- heat recovery.
Within the production route for green steel the objectives of E-ECO Downstream are indicated in the depiction above. Aside of the final assessment, dissemination and eploitation measures the project consists of six working objectives:
Objective 1: Enable currently installed burners to utilize green fuels
The challenge in flexible combustion systems, that allow for blending different fuel gases (renewable and fossil), is the specification of burner for certain fuels. Instead of replacing entire existing burner systems it is aimed to replace burner components by newly 3D-printed designs in order to enable green fuel utilization in reheating furnaces. The analysis and parametric optimal redesign of nozzles, flame stabilizers and swirl plates will be supported by active learning techniques.
Objective 2: Elaboration of hybrid heating concepts to increase fuel flexibility
In downstream reheating processes before further processing is crucial for the final product quality while being very energy-intensive at the same time. Electrical inductive heating represents an alternative to combustion heating, but lacks the high temperatures necessary to be applied in all formats and steel grades. A hybrid heating concept will be developed to reduce CO2 emission by combining electric heating and hydrogen combustion. Testing and assessment in a pilot walking beam furnace will provide the required KPIs for stakeholders to make informed decisions towards sustainable carbon neutral solutions.
Objective 3: Improved logistics to decrease heat loss and increase energy efficiency
Hot charging is remarkable option for reducing CO2 emissions when casting and hot rolling mill are directly connected. To make the application available for disconnected systems a logistical solution is sought. Hot charge technologies and their logistical handling are investigated, thermal losses modelled and loss reducing techniques identified. Finally, fuel savings and CO2 emission reduction will be demonstrated with respect to production mixes and management of rolling programs.
Objective 4: Adapt waste heat recovery systems to future fuel boundary conditions for increased energy efficiency
Due to the change in gas compositions towards hydrogen fuels the H2O content in the exhaust gas will increase as well as the reactivity and thus, modifications to the existing recuperators and regenerator systems for heat recovery are required. The change in waste heat streams in the future downstream processes needs to be incorporated in decarbonisation concepts to guarantee overall efficient (re-)heating.
Objective 5: Implementation timeline
The developed and investigated solutions will be assessed under technical, economic, and ecological point of view to evaluate their applicability. An implementation timeline for the investigated decarbonization technologies/solutions and process adaptations to enhance existing steel making plants for the transition to decarbonisation will be generated on European level.
Objective 6: Dissemination of project results among relevant stakeholders to maximize impact and benefits
Based on the identification of primary and secondary target groups worth exploitation results will be disseminated following a defined dissemination plan. Furthermore, related or competitive technology trends will be carefully monitored as well as a stakeholder analysis will be performed and revised along the project. Thus, the benefits of project results can be maximised by improving the ecological, technological, economic and social impacts.
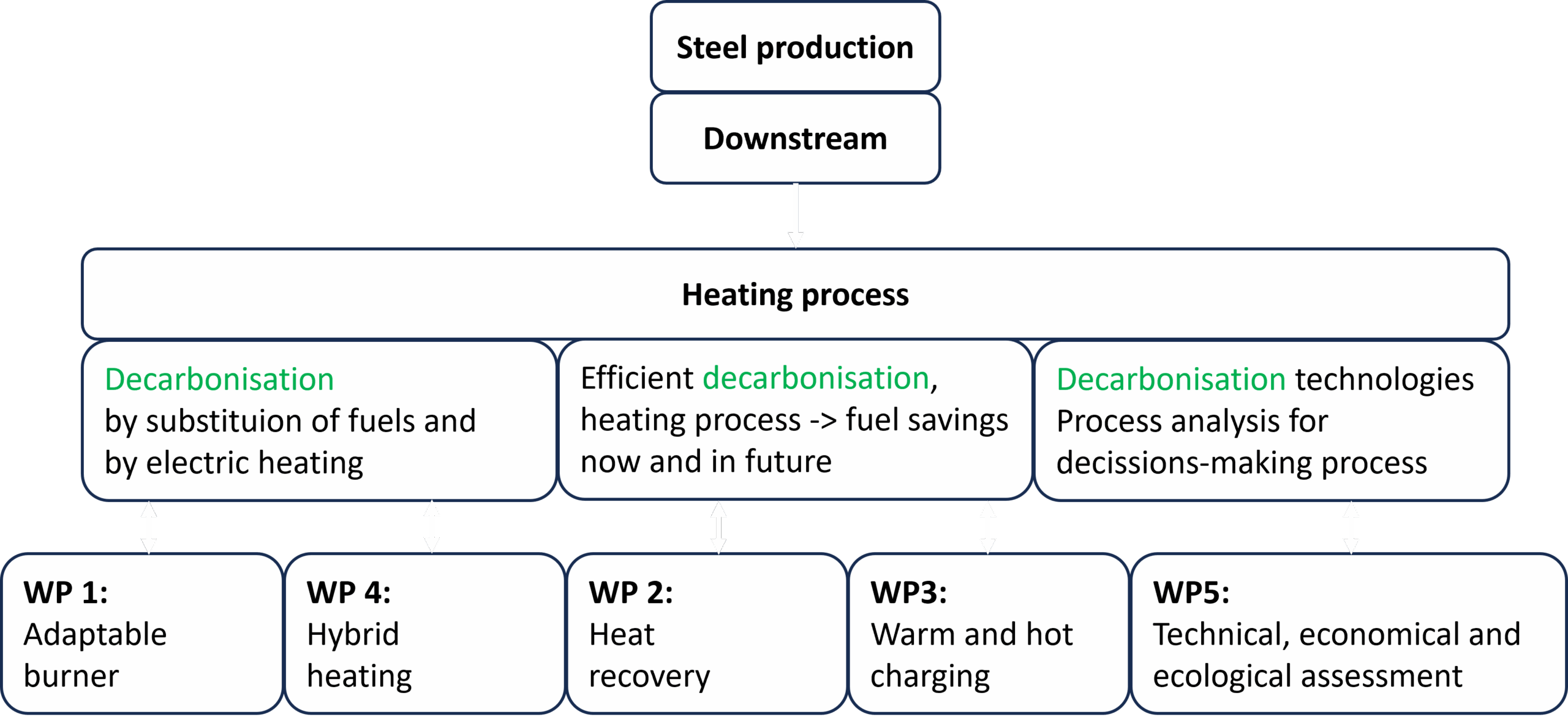
Mission
The methodology of E-ECO Downstream consists of cost-efficient and flexible optimization strategies to decarbonize steel making downstream processes during the transition to fossil carbon free heating of reheating furnaces.
Solutions will be developed by applying computational simulations, experimental investigations in laboratories and at testing facilities under near-service conditions as well as theoretical studies based on real operation data from industrial plants.
The main focus of the investigation and targeted solutions are:
-
- the adaption of processes to new fuels,
- ensuring product quality and productivity,
- fuel flexibility and
- increasing energy efficiency.
Methods for objective 1:
To enable currently installed burners to utilize green fuels new components for the burners will be designed, 3-D printed, integrated into currently used standard burners and investigated under near-service conditions. The development process will include the application of new high temperature resistant metal powders for 3-D printing and investigations in printing and manufacturing these burner parts. The applied methods are:
-
- numerical simulation and modelling of heat transfer, fluid dynamics and combustion as well as thermodynamics. The simulation studies for burner development and 3-D printing are accompanied by artificial intelligence systems,
- experimental investigations of fuel flexible burners at pilot scale and/or near service conditions,
- lab scale experiments to investigate and understand the influence of hydrogen combustion on product and furnace.
Methods for objective 2:
For the elaboration of hybrid heating concepts to increase fuel flexibility electrical heating and H2 combustion are investigated under near-service conditions in a pilot walking beam furnace. The applied methods are:
-
- Numerical simulations for heat transfer and procdess modelling,
- experimental investigations of product heating at near-service conditions in a pilot walking beam furnace,
- lab scale experiments and modelling for detailed understanding of hybrid heating influence on the product.
Methods for objective 3:
The hot and warm charging as improved logistics between casting and reheating furnace to decrease heat loss and increase energy efficiency is investigated theoretically. The applied methods are:
-
- Thermodynamic and process modelling of hot and warm charging applications for plant configuration of producers in this project.
Methods for objective 4:
To adapt waste heat recovery systems to future fuel boundary conditions for increased energy efficiency waste heat recovery in reheating furnaces, the waste heat recovery must be reevaluated. The fuel transition will change the waste heat streams (in temperature, capacity, and composition) in future downstream processes. This will be done by process analysis focused on the involved industrial facilities, development of concepts for waste heat recovery from the selected sources and pilot testing of recuperators and regenerators. The applied methods are:
-
- Thermodynamic modelling and process simulation of heat recovery systems for fuels in transition and future fuels,
- experimental investigations of heat recovery from off-gas at pilot scale with new recuperator and regenerator system for fossil free fuels and oxidizers.
Methods for objective 5 for LCA and retrofit analysis by applying new technologies in European steel plants are mainly theoretical and analytical calculations and studies.