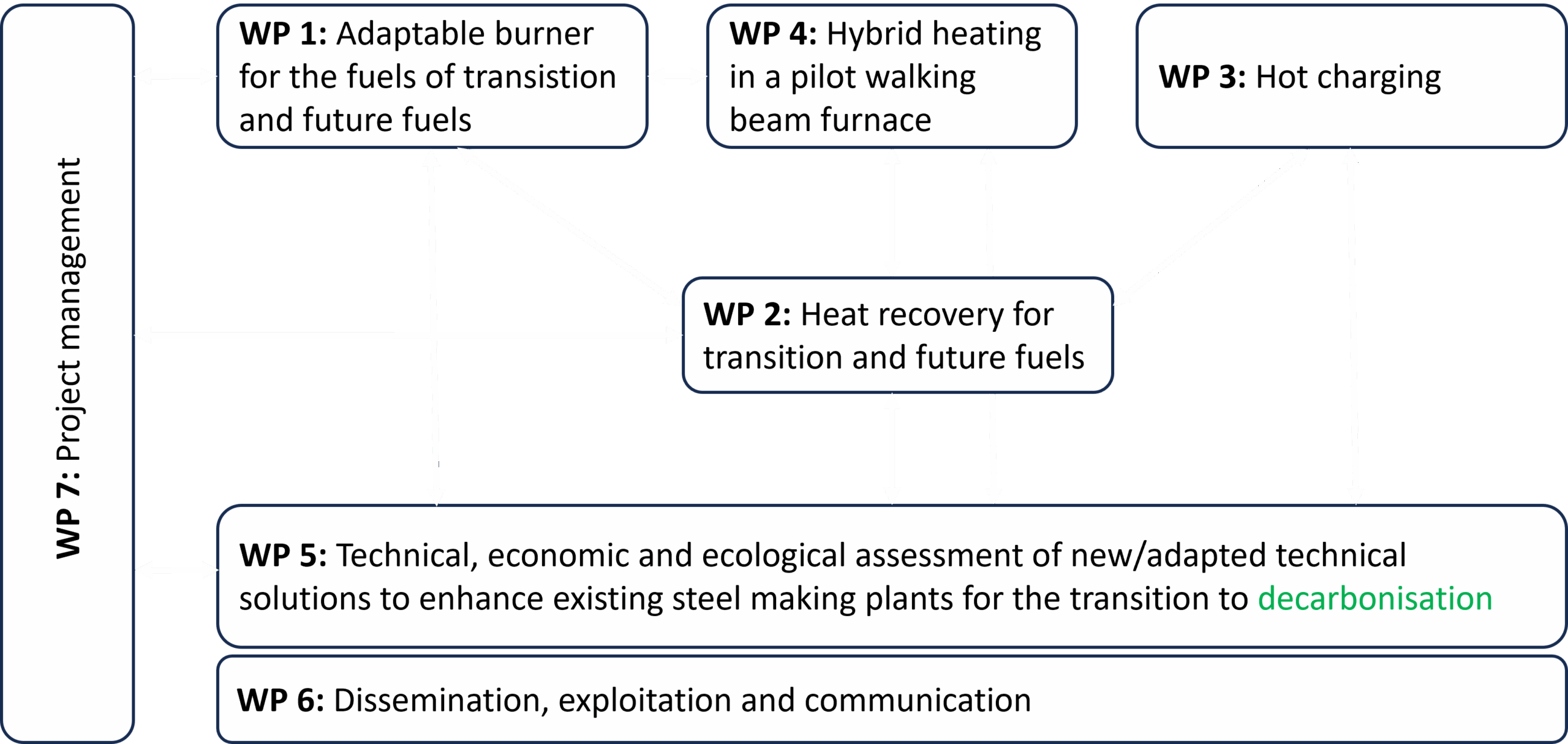
Work Program
E-ECO Downstream is structured systematically by incremental but iterative work phases and consists of 7 Work Packages (WPs). The WPs 1 – 4 are focussed on new and improved technical solutions and are dealing with decarbonization measures by enabling existing burners to new fuels (WP 1), increasing fuel flexibility (WP 4) and energy efficiency (WP 3) as well es adapting waste heat recovery (WP 2) to the changing boundary conditions when using new fuels in the downstream processes. WP 5 will use results from the first four WPs for a technical, economic, and ecological assessment and will define an implementation timeline. The Dissemination, Exploitation and Communication WP (WP 6) is designed to maximise the impact of the results, whereas the project management & coordination (WP 7) will ensure efficient management of the project. Figure 7 Shows the structure of the project and the interrelation of the 7 WPs.
Outcomes
The expected outcomes of investigations and developments in the project are:
Outcome 1: New products (newly designed and 3D- printed burner components) for low cost retrofit of existing burners in RHFs to achieve fuel flexibility regarding renewable carbon free fuels in the future.
Outcome 2: Demonstration of hybrid heating of different steel grades from two producers to give project partners insight in the combined H2 combustion and electrical resistive product heating and the impact on the product. Important KPIs for the stakeholders from steel industry will be provided to make informed decisions on this leg in moving towards sustainable carbon neutral solutions for the steel industry.
Outcome 3: Solutions (adjusted and tested recuperator) to adapt waste heat recovery to the changing operating conditions of downstream processes when using future fuel and scenario analyses concerning their feasibility as well as evaluation of strategical investment opportunities.
Outcome 4: Modelling study of warm and hot charging with hybrid heating to predict the CO2 savings for producers by production modification as relevant information for future decision-making processes in production planning.
Outcome 5: Roadmap and implementation timeline as support for decision makers: Support of decision makers (policymakers and in industry) about possibilities for decarbonization of downstream processes, based on detailed technology evaluation and process KPIs (focus for industrial decision makers) as well as barriers and required boundary conditions (focus for policymakers).
Benefits for stakeholders
The benefits for E-ECO Downstream stakeholders are listed with regard to the outcomes:
Steel industry benefits:
-
- Hybrid heating will provide a flexible option to H2 combustion (fuel flexibility) and CCS which will allow companies to see a viable CO2 neutral solution (Outcome 2).
- Increased fuel flexibility by cost-efficient adaption of burners (Outcome 1).
- Hot and warm charging solutions improve energy efficiency, cut cost and save CO2 (Outcome 4).
- Adaption of waste heat recovery to new fuels will increase energy efficiency and will be cost efficient when it is implemented directly during the planning of new plants (Outcome 3).
Manufacturers and H2 supplier:
The new solutions will open up new markets and bring decarbonization technologies to SMEs as customers (Outcome 1 and 2).
Scientists:
will push further RIA and IA based on the developed solutions and will transfer them to other applications and industries (all Outcomes).
Policymakers:
Support of decision makers and defining of boundary conditions for the steel industry to successfully decarbonize the downstream processes (Outcome 5).
Users:
will benefit from green steel to decarbonize their own products (Outcomes 1-4).